We are proud to showcase this large-scale system integration project. The project involved combining several major sets of powder handling equipment with pneumatic conveying to process large quantities of sugar. Raw sugar is ground to fine sugar, blended with whitener then packed for shipment.
This example is part of a series of case studies from our engineering group, which is focused on becoming a market leader in powder-based food processing plants in Australia.
For more information on
granular and powder materials.
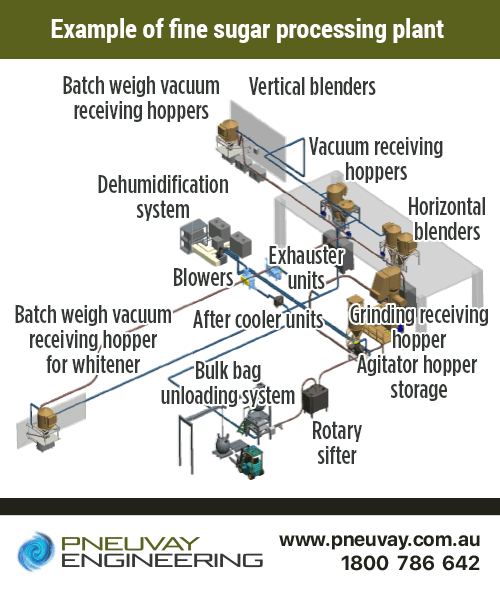
Example of a bulk bag unloading system for raw sugar, grinding, conveying and batch weighing for ground sugar
Bulk bag unloading system for raw sugar for grinding, conveying and batch weighing as fine sugar
This processing plant takes raw sugar and converts it to fine sugar – a process that involves several distinct stages. We shall follow the material flow of the sugar through the processing plant.
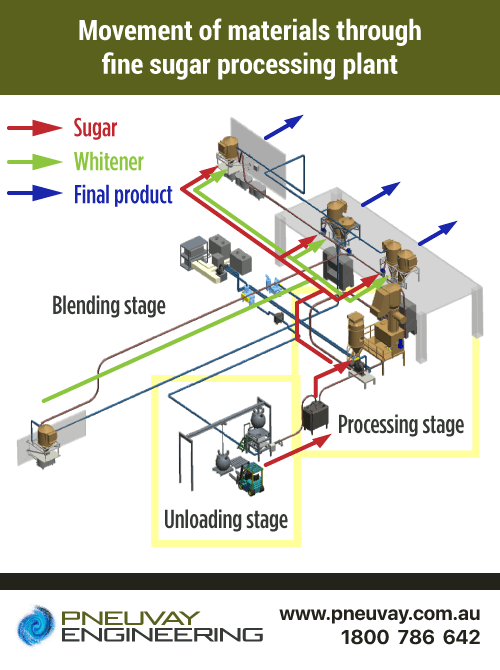
Material flow through fine sugar processing plant
Unloading stage - Raw sugar unloading station
The material flow of sugar in the plant starts with the unloading stage. Unloading of granular materials can occur via several methods. In this case we are using a bulk bag system.Raw sugar is brought to the unloading station in bulk bags that range from 500 kg to 1,500 kg and fed directly into the processing stage. An operator uses an electric hoist to lift and position the bulk bags so each is above a vibratory discharger.
The bulk bag is then shaken so the raw sugar discharges smoothly from the bottom of the bag into a pressure vessel beneath. From there the raw sugar is conveyed pneumatically to the next stage by use of a dense phase pressure system.
The dense phase pressure conveying uses compressed air between 100 to 800 kilo pascals to push the raw sugar through the conveying pipe. It operates on a batch basis, where the pressure vessel is repeatedly filled with raw sugar, pressurised and emptied.
Control panels are used to control the air pressure in the pipe and the speed of the raw sugar to ensure smooth conveying. This batch processing conveyance form is the best solution for the unloading of raw sugar from bulk bags for processing, as the flow needs to be stopped and started with ease.
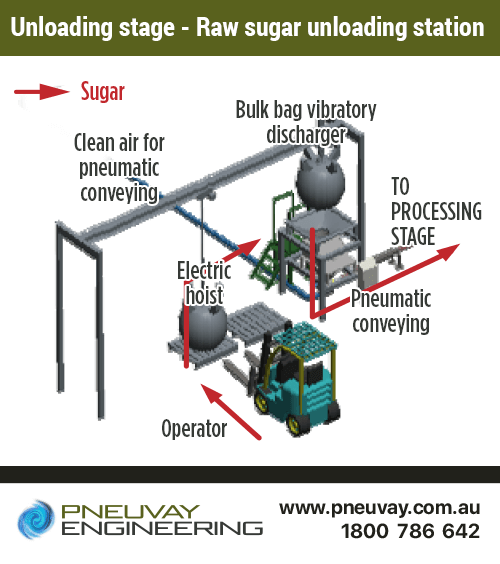
Detailed view of unloading stage
Processing stage - Grinding of sugar
From the unloading stage, the material flow of sugar in the plant continues to a processing stage. The raw sugar is passed through a rotary sifter, where impurities and irregularities are removed.
The sifted raw sugar is then pneumatically conveyed to a receiving hopper, using a dense phase pressure system. This is a temporary storage area that allows a buffer to be formed so it can be discharged into the sugar grinder on a continuous basis.
Once the raw sugar has been ground into fine sugar, it is then stored in an agitator hopper for buffering. The agitation in the hopper prevents bridging or ratholing above the take-away inlet. This ensures a consistent and reliable flow of fine sugar can so it can pneumatically conveyed to the blending stage.
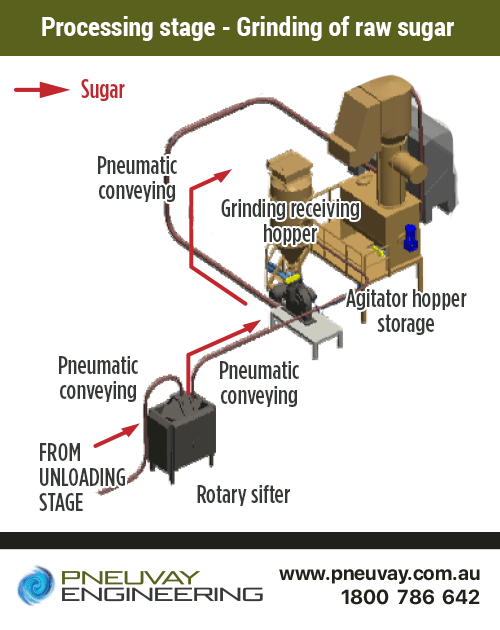
Detailed view of processing stage
Blending stage - Fine sugar and whitener
The material flow of sugar in the plant then moves from the processing stage to the blending stage. The fine sugar is pneumatically conveyed from the agitator hopper to the weighing hoppers on top of the blenders.
Whitener is pneumatically conveyed to weighing hoppers on top of the same blenders. These weighing hoppers batch the sugar and whitener into accurately metered volumes that are then fed into the blenders.
The blending of fine sugar and whitener involves combining them in a gentle fashion so that they become inseparable. The blenders combine fine sugar and whitener from the weighing hoppers according to exact requirements, and the final product is discharged for packaging.
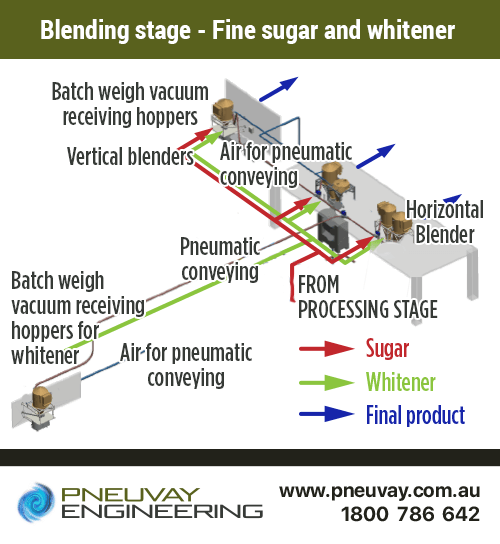
Detailed view of blending stage
Equipment
The systems and components used in the fine sugar processing plant are as follows:
- After-cooler units
- Batch weigh vacuum receiving hoppers
- Batch weigh vacuum receiving hoppers for whitener
- Blowers
- Bulk bag unloading system
- Dehumidification systems
- Exhauster units
- Horizontal blenders
- Sifter
- Vertical blenders
Contact us for assistance
Pneuvay is a leading system integrator for powder handling systems in food processing plants. We cover the Asia-Pacific and Middle East and are expanding into the Australian industry. We service many large food producers and provide best fit and turn key solutions for food processing plants looking to:
- Install new powder material systems
- Expand production capacity
- Upgrade existing powder material systems
If you have any questions in relation to powder material systems for a specific food processing, feel free to call on
1300721458 or
contact us.